6 opportunities to enhance your business with a vinyl cutter
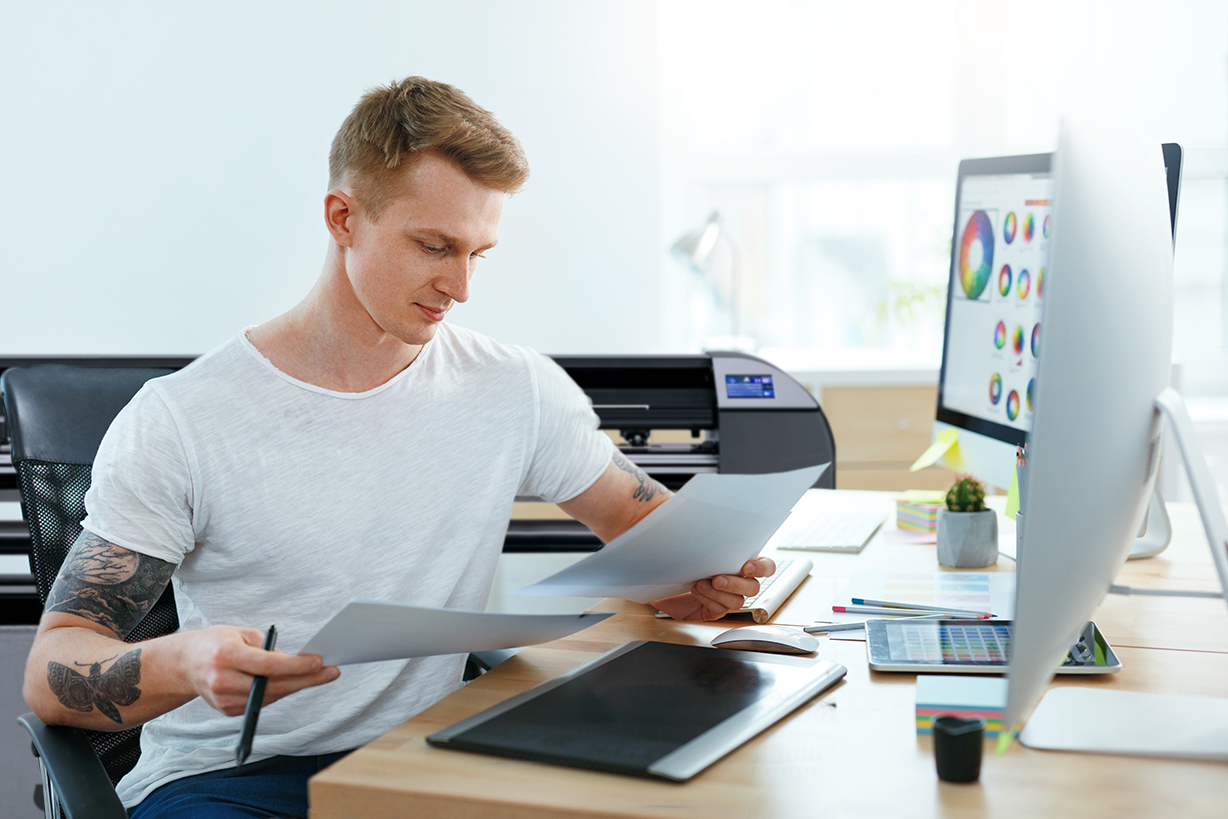
If you weren't convinced already, we will make sure you will be now! Read the following post on 6 reasons to choose our Summa roll cutters above any other available on the market. Obviously, there are more than 6 reasons, but type space is limited, so here we go!
1. True Tangential Technology
A True Tangential head has a motor, controlling the direction of the blade at all times, enabling to cut thick and hard substrates with unsurpassed high detail and quality. Summa offers a True Tangential cutting head, enabling to cut materials quickly and concisely up to 47 mils thick. All other cutters in the market use drag (swivel) cutting heads and an improved process called “Tangential emulation”. Tangential emulation tries to simulate this control but does not have any motorised control over the blade. Consequently, tangential emulation will never provide for the same accuracy than if you were to use a cutter with a True Tangential cutting head.
2. Repeatability
‘Repeatability’ is a term, which refers to how accurately the cutter keeps cutting whilst media is being transported. The repeatability guaranteed on the SummaCut line of cutters is 8 m (26 ft.); on the S Class 2 line, this would be 12 m (40 ft.). The closest competitor in the market only guarantees 1.9 m (6.5 ft.), which is quite a difference. It is important the cutter is able to process the appropriate dimensions accurately at all times, which can be guaranteed with Summa’s repeatability feature. Note: All cutters are measured on a spec called ‘tracking’. However, ‘tracking’ only defines how accurately the transport of the media occurs. This could be misleading because it doesn’t specifically refer to the movement of media whilst cutting.
3. Barcode Feature
Unique to Summa is the ability to read barcodes with the onboard sensor. The barcode will automatically communicate with the software to retrieve the necessary cut data and initiate the cutting. After finishing the job, the cutter will automatically search for the next barcode and repeat the process. This allows for an entire roll of printed graphics to be cut without user intervention. Maximal automation and productivity are yours to enjoy!
4. OPOS Sensor
Summa uses a “white light technology” to recognise registration marks and barcodes. The Summa OPOS (white light) sensor is able to detect registration marks on all UV protection films. Other cutters in the market are still using the old IR (Infra-Red) light. However, all laminates have built-in UV inhibitors nowadays. When using these old IR sensors, the cutter will encounter difficulty to recognise (be able to find) the registration marks because the UV light is being filtered by the UV protected laminate. The OPOS sensor is also capable of registering other colours beyond black on white (dark, blue, grey, etc..).
5. Unique Summa Line: S Class 2 OPOS CAM Series
Summa offers the possibility to have a camera – OPOS CAM – mounted on the cutter instead of a light sensor. The main advantage here is speed. The OPOS CAM system can register marks 10 x faster than any light sensor. This is a considerable increase in productivity, especially when processing entire rolls. Another advantage is the ability to create a “camera profile” for every challenging media type (ie. reflective). This profile will enable the cutter to register marks on any substrate because the profile can be created specifically to the media type.
6. G-Performance, boost your S Class 2 performance up to 40%
Transform your S Class 2 cutter into a lean, mean and faster cutting machine than ever before thanks to the G-Performance feature. No matter whether it be a cutter with tangential or drag knife technology or our smallest or largest cutter in the product range, the G-performance will exceed every model's speed limit. However, speed is not the only advantage you will benefit from. Your S Class 2 cutter will be able to also read registration marks, to achieve a perfect cut, even with print deformations, at an ever faster pace!