Low tech beats high tech
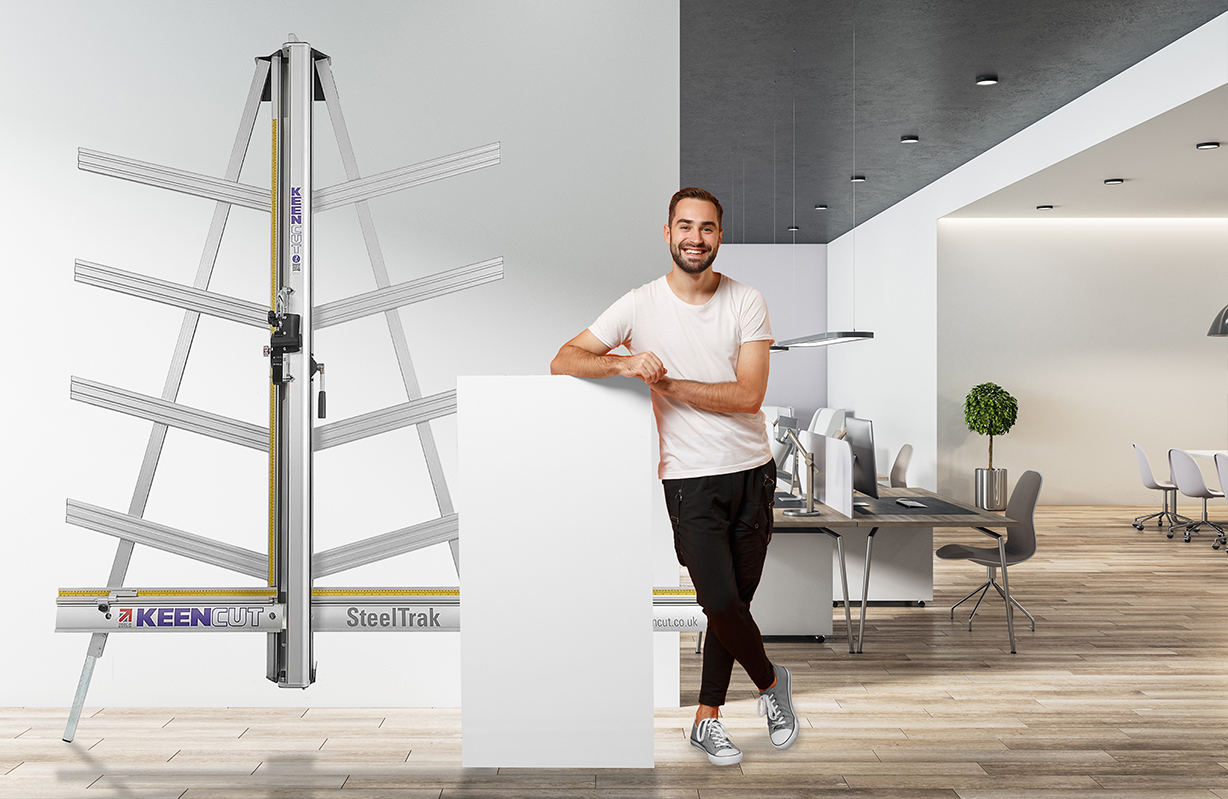
Why is it that, as the market leader in large format print cutters, Keencut does not offer a laser for cutline indication on its vertical machines, but it does use lasers to calibrate Precision Bench Top Cutters?
The answer is quite simple, we design our products so that every feature gives maximum performance and our tests have proven that a simple clear plastic Sightline Strip outperforms a high cost laser every time.
How does the Sightline Strip work?
The Sightline Strip is a clear plastic strip which starts off life wider than it needs to be when it is attached with adhesive to the edge of the clamping bar close to the cut line. The strip is then cut down the length by the blade on the SteelTraK. The result is a precision indicator of exactly where the blade is going to cut. The key thing to understand is that as the edge of the sightline strip is the indicator it has no thickness and therefore pinpoint accurate.
Keencut was the first company to have a cutline indicator on a vertical substrate cutter of this type.
So, why not use a laser? A laser beam is perfectly straight even when fired from here to the moon, surely over a few metres it is going to be super accurate and they are as cheap as a sightline strip.
Yes, they are extremely accurate, that is why we use one to measure the straightness on every single Precision Bench Top Cutter we produce. It is also true that some lasers are very cheap, but it is the computerised measuring equipment we use to control and measure the beams position to within hundredths of a millimetre that costs many thousands of pounds.
Some time ago we carried out a study with the help of a specialist laser company. The only criteria we set was that any solution would not cost the end user any more than £1,000 (on top of the price of the SteelTraK). There were two ways of approaching this: -
The ideal solution is to have a laser line that is bright, well defined and ideally about the thickness of a crop line (we worked on 0.2mm). The ideal position for a laser is suspended above head height a few metres behind the operator so that it can focus a line of red light down the length of the machine. A special lens changes the laser beam into a fan shape and it is the edge of the fan that creates the line. This type of arrangement creates a line that is typically around 1-2mm wide, not fine enough for our purposes and the edge of the line was not sharp enough either, especially when compared to the crisp cut edge of the Sightline Strip.
The width of a crop line is dependant up many things but for our purposes let’s say its 0.2mm. The laser is set back, say, 2m from the SteelTrak, the end of the laser unit only has to move by 0.005mm for it to move the laser line by the thickness of the crop line. How on earth could you calibrate something that fine and ensure it remains accurate despite vibration, expansion/contraction or just general flexing and movement between the SteelTrak and the laser fixing?
So, what if the laser were fixed closer to the machine, for example at the top end of the SteelTrak and the ‘fan’ set to produce a line down the material? The beam would still be 1-2mm wide but there would also be focussing issues as the laser line would be much closer to the lens at the top of the machine than it would at the bottom.
Option two, fasten the laser to the cutting head and align the beam with the cutting line and by moving the cutting head up and down the laser it should accurately give cutline indication along the whole length of the cutter, problem solved…….. or is it?
This is all very well if you just need to align the laser to one crop line and can guarantee your printing is square to the edge of the board and be sure the board itself is perfectly square but what if it is not, just think how this would be done:
So, firstly raise the head to the top of the board and align the crop line with the laser then clamp the board in place, move the cutting head and laser to the bottom to find it is not in line with the bottom crop mark. The problem then is, how can you manoeuvre the bottom end of the board to align to the crop mark and be sure you do not disturb the setting at the top. Quite simply, you cannot be sure, the laser can only be at one crop line or the other.
The Sightline Strip along with the SteelTraK’s unique pressure sensitive clamp makes light work of this situation.
Lightly clamp the board so that it holds the board in place but allows you to rotate and slide the board. Align both crop marks with the edge of the Sightline Strip. Once happy that the alignment is correct, increase the pressure on the clamp and take the cut with full confidence.
Sometimes simplicity does win over expensive technology!
About Keencut
Keencut designs and manufactures manual cutters for the print finishing and picture framing markets, with world-leading accuracy and reliability. Products are sold around the globe to most countries in Europe, the USA, and as far afield as Russia and Australia.
We design and manufacture our entire product range at the Keencut factory in Corby, UK. We use the finest materials and state of the art manufacturing techniques to ensure the highest quality and reliability, and our products come with a minimum five-year comprehensive guarantee plus a minimum 20-year guarantee on all rotating and sliding bearings.
With a broad range of manual cutters, Keencut meets the ever-increasing requirements of customers in the sign-making, large & small format printing, and picture framing industries. Our dedication to finding the ultimate precision engineering solution to each application means that our products have a worldwide reputation as the most accurate, reliable and easy to use.
If you are looking for precision and durability in your cutter, choose Keencut.