EMBRACE NEW POSSIBILITIES
HP Latex 630 / 630W Series
Get your printing needs met and so much more with a printer that delivers more of what you are looking for. Using HP's revolutionary Latex printing technology to produce a wide range of signage, vehicle graphics and decor jobs that look amazing.
UNLOCK POWER
EFFICIENCY AND
PRECISION
EFFICIENCY AND
PRECISION
Onyx V24 RIP Software
UNPARALLED
CUTTING
PERFECTION
Summa S One Series Cutters
ENGINEERED TO PERFORM
Graphtec FC9000 Series
Vinyl Cutters
Vinyl Cutters
Inks and Media
Best Sellers
Latest Products
‹
›
Large Format Printers
Best Sellers
Latest Products
‹
›
We quickly established that PSW were specialists. The installation of our large format scanner went like a dream and it was clear that we were working with experts who new exactly what they were talking about.
John Robertson - Business Owner
We work with PSW when investing in new kit as we trust and like working with them. They understand our business and we have been delighted with all aspects of the service, training and installation they have provided.
Sarah Pittman - Business Owner
From the outset PSW Paper & Print has taken great care to understand our business needs in the fast moving world of large format print. Honest, expert advice and top notch support has resulted in our 10 year relationship.
David Wilson - Business Owner
We quickly established that PSW were specialists. The installation of our large format scanner went like a dream and it was clear that we were working with experts who new exactly what they were talking about.
John Robertson - Business Owner
We work with PSW when investing in new kit as we trust and like working with them. They understand our business and we have been delighted with all aspects of the service, training and installation they have provided.
Sarah Pittman - Business Owner
From the outset PSW Paper & Print has taken great care to understand our business needs in the fast moving world of large format print. Honest, expert advice and top notch support has resulted in our 10 year relationship.
David Wilson - Business Owner
We quickly established that PSW were specialists. The installation of our large format scanner went like a dream and it was clear that we were working with experts who new exactly what they were talking about.
John Robertson - Business Owner
‹
›
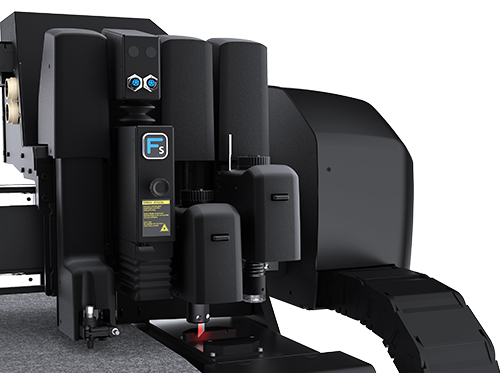

versatility at it's best
Summa’s Professional Flatbed Finishing System is an award-winning solution for producing innovative signage, displays, samples, packaging applications, and more. With an ever increasing arsenal tools and optional add-ons, this is the breakthrough cutting solution you’ve been dreaming about.



